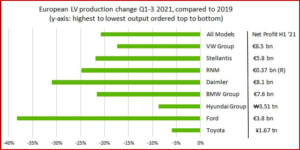
Click to Enlarge.
Optimism by European automakers and analysts, with now wrongful claims that vehicle output would improve markedly in the second half of 2021 are a stark lesson in the resilience of the ongoing COVID-19 pandemic.
The most recent setback has been the forced closure of semiconductor facilities in Malaysia to contain the latest COVID-19 outbreak, the LMC Automotive consultancy notes. This disaster comes from raw material price increases, semiconductor shortages and bottlenecks in the production of intermediate products.
“Undeniably, the major constraint to European Light Vehicle output so far this year has been the scarcity of chips, which is estimated to account for roughly 80% of the total loss in output from our pre-crisis expectations,” said LMC. “Meanwhile, shortages of other vehicle components, such as wiring harnesses and brake parts, have further exacerbated the slowdown, albeit to a lesser extent.”
The usual economic principles no longer apply, or they are upside down. Through to the end of Q3 this year, LMC estimates that almost 1.5 million fewer vehicles were produced in Europe because of chip supply disruptions. “These losses are substantial, so much so that vehicle inventories are running too low to adequately supply buoyant demand for new cars,” said LMC.
This is a significant shift. Vehicle inventories are running too low to supply upbeat demand for new cars. The inverse economic law is usually true: with demand dictating the level of supply. The crisis has increasingly steered market power away from consumers. Indeed Toyota announced today that it will suspend production for several days in Japan during October at 27 lines in 14 plants out of 28 lines in 14 plants.
Nonetheless automakers have improved profitability during the first half of 2021 (see chart above for H1 CY net profit figures) by give precedence to high-margin models and raising vehicle prices to offset higher input costs. Moreover, manufacturers have continued the cost-reduction work started pre-pandemic, including capacity and model line-up rationalizations.
Unfortunately, supply constraints and inflationary pressures will certainly persist until the chip shortage is resolved. This miracle will require greater chip allocation to the automotive industry. But the cost and complex nature of semiconductor manufacturing means that it takes years for production capacity to expand.
“We therefore expect disruptions to European Light Vehicle production to continue until at least 2023, at which point output volumes are set to just about recover to 2019 (pre-pandemic) levels,” said LMC.
European Light Vehicle Production Tanking
Click to Enlarge.
Optimism by European automakers and analysts, with now wrongful claims that vehicle output would improve markedly in the second half of 2021 are a stark lesson in the resilience of the ongoing COVID-19 pandemic.
The most recent setback has been the forced closure of semiconductor facilities in Malaysia to contain the latest COVID-19 outbreak, the LMC Automotive consultancy notes. This disaster comes from raw material price increases, semiconductor shortages and bottlenecks in the production of intermediate products.
“Undeniably, the major constraint to European Light Vehicle output so far this year has been the scarcity of chips, which is estimated to account for roughly 80% of the total loss in output from our pre-crisis expectations,” said LMC. “Meanwhile, shortages of other vehicle components, such as wiring harnesses and brake parts, have further exacerbated the slowdown, albeit to a lesser extent.”
The usual economic principles no longer apply, or they are upside down. Through to the end of Q3 this year, LMC estimates that almost 1.5 million fewer vehicles were produced in Europe because of chip supply disruptions. “These losses are substantial, so much so that vehicle inventories are running too low to adequately supply buoyant demand for new cars,” said LMC.
This is a significant shift. Vehicle inventories are running too low to supply upbeat demand for new cars. The inverse economic law is usually true: with demand dictating the level of supply. The crisis has increasingly steered market power away from consumers. Indeed Toyota announced today that it will suspend production for several days in Japan during October at 27 lines in 14 plants out of 28 lines in 14 plants.
Nonetheless automakers have improved profitability during the first half of 2021 (see chart above for H1 CY net profit figures) by give precedence to high-margin models and raising vehicle prices to offset higher input costs. Moreover, manufacturers have continued the cost-reduction work started pre-pandemic, including capacity and model line-up rationalizations.
Unfortunately, supply constraints and inflationary pressures will certainly persist until the chip shortage is resolved. This miracle will require greater chip allocation to the automotive industry. But the cost and complex nature of semiconductor manufacturing means that it takes years for production capacity to expand.
“We therefore expect disruptions to European Light Vehicle production to continue until at least 2023, at which point output volumes are set to just about recover to 2019 (pre-pandemic) levels,” said LMC.