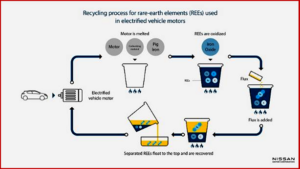
In 2017, Nissan began collaborating with Waseda University, which has a record of researching non-ferrous metal recycling and smelting.
Nissan Motor and Waseda University today announced the start of testing in Japan of a jointly developed recycling process that recovers high-purity rare-earth compounds from electrified vehicle motor magnets. The testing is aimed at enabling practical application of the new process by the mid-2020s. EVs are potentially an ecological and political disaster since they rely on mining, refining and using potentially toxic rare-earth compounds. (Ford – EVs Present Environmental, Human Rights Issues)
Most EV motors in electrified vehicles use neodymium magnets, which contain scarce rare-earth metals such as neodymium and dysprosium. Reducing the use of scarce rare earths is essential not only because of the environmental impact of mining and refining, but also because the shifting balance of supply and demand leads to price fluctuations for both manufacturers and consumers.
To use limited and valuable resources more effectively, since 2010 Nissan says it has been working from the design stage to reduce the amount1 of heavy rare-earth elements (REEs) in motor magnets. In addition, Nissan is recycling REEs by removing magnets from motors that do not meet production standards and returning them to suppliers. Currently, multiple steps are involved, including manual disassembly and removal. Therefore, developing a simpler and more economical process is important to achieve increased recycling in the future.
In 2017, Nissan began collaborating with Waseda University, which has a record of researching non-ferrous metal recycling and smelting. In March 2020 the collaboration developed a pyrometallurgy process that does not require motor disassembly.
Process
- A carburizing material and pig iron are added to the motor, which is then heated to at least 1,400 C and begins to melt.
- Iron oxide is added to oxidize the REEs in the molten mixture.
- A small amount of borate-based flux, which is capable of dissolving rare-earth oxides even at low temperatures and highly efficiently recovering REEs, is added to the molten mixture.
- The molten mixture separates into two liquid layers, with the molten oxide layer(slag) that contains the REEs floating to the top, and the higher density iron-carbon(Fe-C) alloy layer sinking to the bottom.
- The REEs are then recovered from the slag.
1 The Nissan Note e-POWER produced in FY2020 uses magnets with 85% fewer heavy REEs than the Nissan LEAF produced in FY2010.
AutoInformed.com on
Nissan, Waseda U. Testing EV Motor Recycling
In 2017, Nissan began collaborating with Waseda University, which has a record of researching non-ferrous metal recycling and smelting.
Nissan Motor and Waseda University today announced the start of testing in Japan of a jointly developed recycling process that recovers high-purity rare-earth compounds from electrified vehicle motor magnets. The testing is aimed at enabling practical application of the new process by the mid-2020s. EVs are potentially an ecological and political disaster since they rely on mining, refining and using potentially toxic rare-earth compounds. (Ford – EVs Present Environmental, Human Rights Issues)
Most EV motors in electrified vehicles use neodymium magnets, which contain scarce rare-earth metals such as neodymium and dysprosium. Reducing the use of scarce rare earths is essential not only because of the environmental impact of mining and refining, but also because the shifting balance of supply and demand leads to price fluctuations for both manufacturers and consumers.
To use limited and valuable resources more effectively, since 2010 Nissan says it has been working from the design stage to reduce the amount1 of heavy rare-earth elements (REEs) in motor magnets. In addition, Nissan is recycling REEs by removing magnets from motors that do not meet production standards and returning them to suppliers. Currently, multiple steps are involved, including manual disassembly and removal. Therefore, developing a simpler and more economical process is important to achieve increased recycling in the future.
In 2017, Nissan began collaborating with Waseda University, which has a record of researching non-ferrous metal recycling and smelting. In March 2020 the collaboration developed a pyrometallurgy process that does not require motor disassembly.
Process
1 The Nissan Note e-POWER produced in FY2020 uses magnets with 85% fewer heavy REEs than the Nissan LEAF produced in FY2010.
AutoInformed.com on