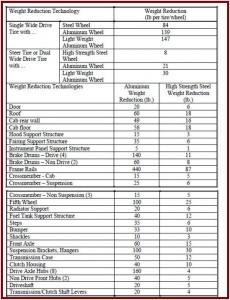
Automakers and truckmakers don’t buy materials like you buy food by looking for the lowest cost per pound.
At first glance it appears to be a battle of the press releases as the steel and aluminum industries vie for contracts on new vehicles to reduce weight. Since virtually all cars and trucks right up to Class 8 big rigs will need to get lighter under increasingly stringent fuel economy rules, decade’s old sourcing patterns – and billions of dollars in future steel and aluminum contracts – are at stake.
The latest data comes from Alcoa (NYSE:AA). Alcoa says the aluminum industry will play a major role in the new effort to reduce GHG emissions and increase fuel efficiency for medium and heavy trucks and buses announced last week by the Environmental Protection Agency (EPA) and the National Highway Traffic Safety Administration. (See President Obama to Announce First Fuel Economy Regulations for Heavy Trucks, Buses. $50 Billion in Fuel Savings Claimed)
The Department of Energy said that aluminum has potential to reduce mass by 40-60%. A study conducted by Alcoa shows the potential to save 3,500 to 4,500 pounds across a tractor-trailer combination through the increased use of aluminum in frame rails, wheels, and fifth wheels.
Based on this Alcoa and Aluminum Association data, the federal agencies developed an expanded list of weight reduction opportunities for the final rulemaking. A table published shows nearly 30 technologies and the potential weight savings of each using aluminum or steel. In nearly each instance the savings from aluminum is at least twice that of steel and in some instances the benefits of aluminum are five times those of steel.
For example using aluminum to develop frame rails for a truck, instead of the steel currently used, would save 440 pounds while using high-strength steel would save 87 pounds. And brake drums made of aluminum would save 140 pounds compared with 11 pounds of savings from steel.
However, the ongoing fight about which material to use isn’t necessarily that clear cut. On a pound for pound basis, there’s not much of a price difference between advanced high strength steels (about 50% of the steel in a current vehicle is AHSS) and aluminum.
However, automakers and truckmakers don’t buy materials like you buy food by looking for the lowest cost per pound. That’s because vehicles are complex systems, and removing weight in one are can have compounding effects by allowing for the downsizing of other components such as engines and some federal studies on improving fuel economy have been controversial, particularly with assumptions that weight reduction is free, along with the fact that they are not peer reviewed, and assumptions are often not stated. (See $10,000 Increase per Auto Under Fuel Economy Proposal? And Tougher Vehicle Economy Standards to Save Billions in Costs?)
Needless to say the steelmakers have their own view of the matter:
“When one considers the total vehicle life cycle, steel is the most environmentally effective choice for automakers due to its relatively low energy and emissions during the manufacturing phase, significant mass reduction during the driving phase, and 100% recyclability at the end of the vehicle’s life,” according to the AISI, aka the American Iron and Steel Institute.
“The use of current grades of AHSS can reduce a vehicle’s structural weight by as much as 25% and can cut total life cycle CO2 emissions by up to 15% more than any other automotive material. With continued steel and technology developments, greater efficiencies will be realized,” AISI said.