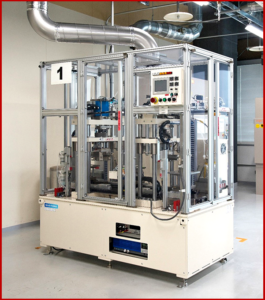
Toyota is also providing its patents and expertise to vacuum press manufacturer Mikado Technos, which has incorporated its own technologies to develop and manufacture a stamping-type plating machine for sale through Kanematsu.
As the world swelters and arctic fires burn uncontrolled, Toyota Motor Corporation is reducing CO2. Toyota is using the world’s first stamping-type plating technology that has a polymer membrane (solid electrolyte membrane), through which metal ions can pass, to apply plating only to areas requiring it. The technology is used in the plating process for forming copper, nickel, and other metal coatings on substrates during the manufacturing of electronic parts.
This new stamping-type plating machine eliminates the need of a dipping process where parts to be plated are completely immersed in multiple baths of plating solution, which is required in the most common plating processes at present. As a result, waste solution can be dramatically reduced to about one-thirtieth and CO2 emissions to about one-third, which contributes to a significant reduction in environmental impact. The technology also reduces plating time and the process footprint.
Toyota has also announced a collaboration with Mikado Technos Co., Ltd. and Kanematsu Corporation to manufacture, sell and expand the use of new plating machines based on this technology.
During the next two to three years, Toyota hopes to sell the stamping-type plating machine to several companies as a test machine for verification and evaluation. Then, from 2023 or 2024, with the aim of achieving widespread use, it will expand sales more broadly for general users as a full production machine.
Toyota decided to launch the stamping-type plating machine, which is expected to deliver these outcomes, and expand use to many companies in a range of industries not just to its business partners in the production of Toyota automobiles, to help reduce the impact on the environment and provide other benefits.
The newly developed stamping-type plating machine has a head, with the upper part filled with solution, and a solid electrolyte membrane, through which metal ions pass, mounted to the tip of the head that is pressed against the area to be plated. Hence the stamping name. This structure enables the solid electrolyte membrane, which is mounted to the tip of the head, to be pressed against only that part of the substrate that requires plating. When the electric current flows, the metal plating is applied, like a stamping but only to the area in contact with the membrane.
In the conventional plating process, however, substrates are completely immersed in solutions of copper, nickel or other plating metal and the metal film (plating) is created when the electric current flows. Multiple large baths for dipping the complete substrates are required for this and substrate washing processes before and after plating. Large amounts of plating solution must also be used because the complete substrates must be immersed in the baths, which means that large amounts of plating solution must also be discarded (wasted) after use. The entire plating process, including the equipment for removing toxic substances released into the air and for treating large amounts of waste solution, can be extensive.
Toyota announced the Plant Zero CO2 Emissions Challenge as part of the Toyota Environmental Challenge 2050, an initiative to contribute to the creation of a sustainable society, which is part of a set of 17 goals for achieving a sustainable society. The Toyota Group will work together to fulfill this challenge, adopting stamped plating machines within the Group and steadily reducing the amount of CO2 it emits during its production processes.
About Ken Zino
Ken Zino, publisher (kzhw@aol.com), is a versatile auto industry participant with global experience spanning decades in print and broadcast journalism, as well as social media. He has automobile testing, marketing, public relations and communications experience. He is past president of The International Motor Press Assn, the Detroit Press Club, founding member and first President of the Automotive Press Assn. He is a member of APA, IMPA and the Midwest Automotive Press Assn.
Zino is at home on test tracks, knows his way around U.S. Congressional hearing rooms, auto company headquarters, plant floors, as well as industry research and development labs where the real mobility work is done. He can quote from court decisions, refer to instrumented road tests, analyze financial results, and profile executive personalities and corporate cultures.
He also brings an historical perspective while citing their contemporary relevance of the work of legendary auto writers such as Ken Purdy, Jim Dunne or Jerry Flint, or writers such as Red Smith, Mark Twain, Thomas Jefferson – all to bring perspective to a chaotic automotive universe.
Above all, decades after he first drove a car, Zino still revels in the sound of the exhaust as the throttle is blipped and the driver’s rush that occurs when the entry, apex and exit points of a turn are smoothly and swiftly crossed. It’s the beginning of a perfect lap.
AutoInformed has an editorial philosophy that loves transportation machines of all kinds while promoting critical thinking about the future use of cars and trucks.
Zino builds AutoInformed from his background in automotive journalism starting at Hearst Publishing in New York City on Motor and MotorTech Magazines and car testing where he reviewed hundreds of vehicles in his decade-long stint as the Detroit Bureau Chief of Road & Track magazine. Zino has also worked in Europe, and Asia – now the largest automotive market in the world with China at its center.
Toyota Plating Machine Significantly Reduces CO2
Toyota is also providing its patents and expertise to vacuum press manufacturer Mikado Technos, which has incorporated its own technologies to develop and manufacture a stamping-type plating machine for sale through Kanematsu.
As the world swelters and arctic fires burn uncontrolled, Toyota Motor Corporation is reducing CO2. Toyota is using the world’s first stamping-type plating technology that has a polymer membrane (solid electrolyte membrane), through which metal ions can pass, to apply plating only to areas requiring it. The technology is used in the plating process for forming copper, nickel, and other metal coatings on substrates during the manufacturing of electronic parts.
This new stamping-type plating machine eliminates the need of a dipping process where parts to be plated are completely immersed in multiple baths of plating solution, which is required in the most common plating processes at present. As a result, waste solution can be dramatically reduced to about one-thirtieth and CO2 emissions to about one-third, which contributes to a significant reduction in environmental impact. The technology also reduces plating time and the process footprint.
Toyota has also announced a collaboration with Mikado Technos Co., Ltd. and Kanematsu Corporation to manufacture, sell and expand the use of new plating machines based on this technology.
During the next two to three years, Toyota hopes to sell the stamping-type plating machine to several companies as a test machine for verification and evaluation. Then, from 2023 or 2024, with the aim of achieving widespread use, it will expand sales more broadly for general users as a full production machine.
Toyota decided to launch the stamping-type plating machine, which is expected to deliver these outcomes, and expand use to many companies in a range of industries not just to its business partners in the production of Toyota automobiles, to help reduce the impact on the environment and provide other benefits.
The newly developed stamping-type plating machine has a head, with the upper part filled with solution, and a solid electrolyte membrane, through which metal ions pass, mounted to the tip of the head that is pressed against the area to be plated. Hence the stamping name. This structure enables the solid electrolyte membrane, which is mounted to the tip of the head, to be pressed against only that part of the substrate that requires plating. When the electric current flows, the metal plating is applied, like a stamping but only to the area in contact with the membrane.
In the conventional plating process, however, substrates are completely immersed in solutions of copper, nickel or other plating metal and the metal film (plating) is created when the electric current flows. Multiple large baths for dipping the complete substrates are required for this and substrate washing processes before and after plating. Large amounts of plating solution must also be used because the complete substrates must be immersed in the baths, which means that large amounts of plating solution must also be discarded (wasted) after use. The entire plating process, including the equipment for removing toxic substances released into the air and for treating large amounts of waste solution, can be extensive.
Toyota announced the Plant Zero CO2 Emissions Challenge as part of the Toyota Environmental Challenge 2050, an initiative to contribute to the creation of a sustainable society, which is part of a set of 17 goals for achieving a sustainable society. The Toyota Group will work together to fulfill this challenge, adopting stamped plating machines within the Group and steadily reducing the amount of CO2 it emits during its production processes.
About Ken Zino
Ken Zino, publisher (kzhw@aol.com), is a versatile auto industry participant with global experience spanning decades in print and broadcast journalism, as well as social media. He has automobile testing, marketing, public relations and communications experience. He is past president of The International Motor Press Assn, the Detroit Press Club, founding member and first President of the Automotive Press Assn. He is a member of APA, IMPA and the Midwest Automotive Press Assn. Zino is at home on test tracks, knows his way around U.S. Congressional hearing rooms, auto company headquarters, plant floors, as well as industry research and development labs where the real mobility work is done. He can quote from court decisions, refer to instrumented road tests, analyze financial results, and profile executive personalities and corporate cultures. He also brings an historical perspective while citing their contemporary relevance of the work of legendary auto writers such as Ken Purdy, Jim Dunne or Jerry Flint, or writers such as Red Smith, Mark Twain, Thomas Jefferson – all to bring perspective to a chaotic automotive universe. Above all, decades after he first drove a car, Zino still revels in the sound of the exhaust as the throttle is blipped and the driver’s rush that occurs when the entry, apex and exit points of a turn are smoothly and swiftly crossed. It’s the beginning of a perfect lap. AutoInformed has an editorial philosophy that loves transportation machines of all kinds while promoting critical thinking about the future use of cars and trucks. Zino builds AutoInformed from his background in automotive journalism starting at Hearst Publishing in New York City on Motor and MotorTech Magazines and car testing where he reviewed hundreds of vehicles in his decade-long stint as the Detroit Bureau Chief of Road & Track magazine. Zino has also worked in Europe, and Asia – now the largest automotive market in the world with China at its center.