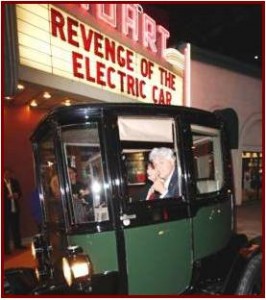
Another twist on the revenge of the electric car? Taxpayers keep sending money to solve long-standing range and design issues.
Two research teams from the University of Maryland Energy Research Center were awarded grants from U.S. taxpayers via the Advanced Research Projects Agency-Energy (ARPA-E) to develop EV batteries using innovative chemistries, architectures and designs.
The two University of Maryland, aka UMD, taxpayer funded projects were among 22 selected nationwide that received a total of $36 million in research funding from ARPA-E’s new program, Robust Affordable Next Generation Energy Storage Systems (RANGE), which aims to accelerate widespread EV adoption by dramatically improving driving range and reliability, and by providing low-cost, low-carbon alternatives to today’s vehicles.
Lithium-ion batteries are problematic in electric vehicles due to short driving range, high cost, and low safety and reliability. Researchers at UMD and Army Research Lab (ARL) will work together to develop a hybridized ions aqueous battery that could cut the Li-ion battery system cost in half and would enable an EV to travel two times as long per charge.
The University of Maryland team will attempt to make a critical breakthrough in improving the energy density of an aqueous battery by doubling the cell voltage from 1.2 V to 2.5-3.0V and doubling the capacity using intercalation chemistries by the twin ions. If successful, UMD’s aqueous battery would make EVs cost and safety-competitive and travel 300 miles on a single charge.
LMD also claims it will develop ceramic materials and processing methods to enable high-power, solid-state, lithium-ion batteries. Most lithium-ion batteries are liquid based, but solid-state batteries have a greater abuse tolerance that reduces the need for heavy protective components. UMD claims it will use multi-layer ceramics processing methods to produce a solid-state battery pack with lower weight and longer life.
“Due to their all solid state construction, these lithium-ion batteries are non-flammable and intrinsically safe,” said Prof. Wachsman of UMD. “Moreover due to their novel highly conductivity materials and fabrication methods will exceed current goals for electric vehicle range, acceleration, and cost.”