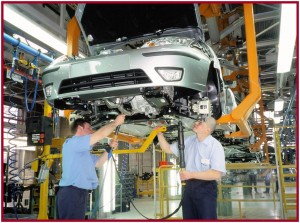
Ford, the first foreign automaker to start producing cars in Russia back in 2002, has closed the plant.
The assault on traditional auto plant business models continues unabated with vehicle ownership arrangements and customer preferences changing. The conventional wisdom among most industry observers is that vehicle ownership has peaked and will be replaced by different types of transportation, such as carpooling or ride sharing apps like Lyft and Uber. There is also a drastic shift in regulation and the growth of cycling, electric bikes, scooters and other forms of personal transportation.
So whither auto plants with their well-paid, highly skilled and heavily unionized work? Plant closures and retrenchments in several countries is worrying for unions.
The need to transition from a carbon-based economy is clear. Some governments have now announced gasoline and diesel bans in the future. Never mind that electric vehicles, ala Google, Lyft, Uber, Tesla, and the infrastructure needed for them, are not ready for mass adoption. Yet. (EVs have fewer moving parts than those with internal combustion engines and require fewer workers. IG Metall in Germany expects the loss of 160,000 jobs due to electrified vehicles.)
“While we need to fight closures plant by plant, we also need to understand the wider structural drivers,” says the global union IndustriALL. It correctly notes that automakers are using the intense transformation of the business to close or consolidate both unprofitable auto plants as well as profitable operations with slim margins.
In its view, General Motors is an extreme example. GM has closed a plant in Australia, sold its operations in Europe, Russia and Africa, and will close four plants in the US and one in Canada this year at a cost of almost 6,000 jobs. (see GM Rejects Unifor Proposals for Oshawa Plant Closing GM to Federal and Ontario Governments – Oshawa Doomed)
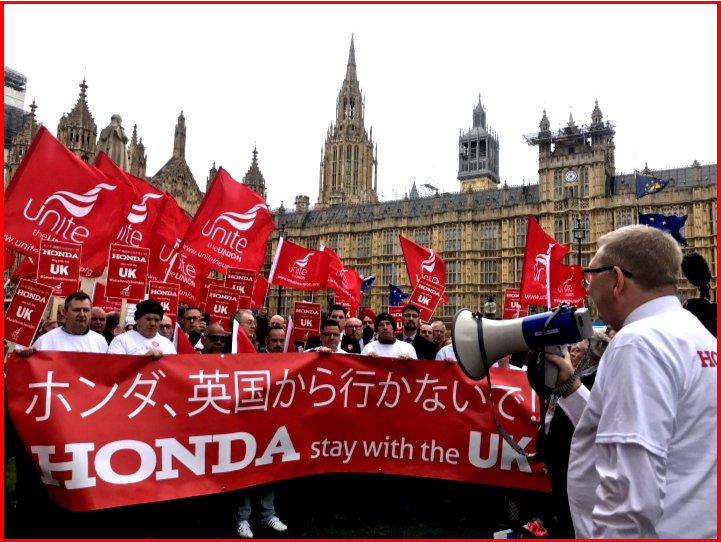
Unite GS Len McCluskey Addresses Workers – Courtesy IndustriALL
Honda has announced that it will close its factory in Swindon, UK, with the loss of 3,500 jobs, and discontinue production of the Civic in Gebze, Turkey, affecting 1,000 workers. (Brexit Panic Takes Hold. Auto Industry Urges – Begs? – Negotiators to Avert the Business Killing Worst-Case Scenario and No Deal Brexit to Cost UK Auto Sector £9 Billion Per Year)
Jaguar Land Rover will cut 4,500 jobs globally, and Nissan cancelled plans to build its new SUV in the UK. Ford is reviewing its operations in Europe and announced that it will close the São Bernardo plant in Brazil, with the loss of 3,000 jobs. (Ford to Restructure European Business Once Again, Weak Ford 2018 Financial Results Prove Need for Shakeup Ford Exits Heavy Truck Business in South America, Unions Protest Closing of Ford Plant Leningrad Region)
“This is a major global restructuring: the industry needs massive investment to shift to the next stage. We need to be part of part of the conversation about managing this change,” notes IndustriALL.
Industry 4.0 – The Future of Work
Auto manufacturing is already highly automated, with robots doing a significant amount of the work. A new generation of electric and autonomous vehicles will mean the design of new, completely integrated systems, covering every process along the supply chain. Highly skilled workers will still be needed for assembly and machine maintenance, but a lot of auxiliary jobs will be gone.
Solutions?
“Without intervention, the auto plants of the future will employ far fewer workers than they do today. While the principles of managing change in industry are familiar, unions must do a lot of focused work to develop credible plans,” says IndustriALL.
IndustriALL has global framework agreements with several auto companies. These enable high level discussions about the future of the industry and provide an opportunity to negotiate the transition to new forms of production.
Lobby
Unions as always must work with governments to develop sustainable industrial policy and not wait for companies to create jobs. Infrastructure, transport policy and urban planning are significant. The way cities are designed has major implications for the future of transport.
“Unions need to prepare for the new world of work. The competence of highly skilled auto workers needs to be preserved and developed to cater for the needs of the future auto industry, but also, when closures are unavoidable, for the needs of new industries that will fill the void. This work will have to be done in cooperation with companies and local and national governments,” says IndustriALL.
Over the course of this year, IndustriALL will host a series of meetings designed to develop best practice from affiliates who have experience of these changes.
As well as a series of company-specific network meetings, an expert meeting on changes in the industry will be held this year. In December, this will culminate in an IndustriALL auto meeting where recommendations for dealing with changes in the sector will be discussed.
IndustriALL Endorses Global Agreements to Fight and Shape Policy on the Growing Number of Auto Plant Closures
Ford, the first foreign automaker to start producing cars in Russia back in 2002, has closed the plant.
The assault on traditional auto plant business models continues unabated with vehicle ownership arrangements and customer preferences changing. The conventional wisdom among most industry observers is that vehicle ownership has peaked and will be replaced by different types of transportation, such as carpooling or ride sharing apps like Lyft and Uber. There is also a drastic shift in regulation and the growth of cycling, electric bikes, scooters and other forms of personal transportation.
So whither auto plants with their well-paid, highly skilled and heavily unionized work? Plant closures and retrenchments in several countries is worrying for unions.
The need to transition from a carbon-based economy is clear. Some governments have now announced gasoline and diesel bans in the future. Never mind that electric vehicles, ala Google, Lyft, Uber, Tesla, and the infrastructure needed for them, are not ready for mass adoption. Yet. (EVs have fewer moving parts than those with internal combustion engines and require fewer workers. IG Metall in Germany expects the loss of 160,000 jobs due to electrified vehicles.)
“While we need to fight closures plant by plant, we also need to understand the wider structural drivers,” says the global union IndustriALL. It correctly notes that automakers are using the intense transformation of the business to close or consolidate both unprofitable auto plants as well as profitable operations with slim margins.
In its view, General Motors is an extreme example. GM has closed a plant in Australia, sold its operations in Europe, Russia and Africa, and will close four plants in the US and one in Canada this year at a cost of almost 6,000 jobs. (see GM Rejects Unifor Proposals for Oshawa Plant Closing GM to Federal and Ontario Governments – Oshawa Doomed)
Unite GS Len McCluskey Addresses Workers – Courtesy IndustriALL
Honda has announced that it will close its factory in Swindon, UK, with the loss of 3,500 jobs, and discontinue production of the Civic in Gebze, Turkey, affecting 1,000 workers. (Brexit Panic Takes Hold. Auto Industry Urges – Begs? – Negotiators to Avert the Business Killing Worst-Case Scenario and No Deal Brexit to Cost UK Auto Sector £9 Billion Per Year)
Jaguar Land Rover will cut 4,500 jobs globally, and Nissan cancelled plans to build its new SUV in the UK. Ford is reviewing its operations in Europe and announced that it will close the São Bernardo plant in Brazil, with the loss of 3,000 jobs. (Ford to Restructure European Business Once Again, Weak Ford 2018 Financial Results Prove Need for Shakeup Ford Exits Heavy Truck Business in South America, Unions Protest Closing of Ford Plant Leningrad Region)
“This is a major global restructuring: the industry needs massive investment to shift to the next stage. We need to be part of part of the conversation about managing this change,” notes IndustriALL.
Industry 4.0 – The Future of Work
Auto manufacturing is already highly automated, with robots doing a significant amount of the work. A new generation of electric and autonomous vehicles will mean the design of new, completely integrated systems, covering every process along the supply chain. Highly skilled workers will still be needed for assembly and machine maintenance, but a lot of auxiliary jobs will be gone.
Solutions?
“Without intervention, the auto plants of the future will employ far fewer workers than they do today. While the principles of managing change in industry are familiar, unions must do a lot of focused work to develop credible plans,” says IndustriALL.
IndustriALL has global framework agreements with several auto companies. These enable high level discussions about the future of the industry and provide an opportunity to negotiate the transition to new forms of production.
Lobby
Unions as always must work with governments to develop sustainable industrial policy and not wait for companies to create jobs. Infrastructure, transport policy and urban planning are significant. The way cities are designed has major implications for the future of transport.
“Unions need to prepare for the new world of work. The competence of highly skilled auto workers needs to be preserved and developed to cater for the needs of the future auto industry, but also, when closures are unavoidable, for the needs of new industries that will fill the void. This work will have to be done in cooperation with companies and local and national governments,” says IndustriALL.
Over the course of this year, IndustriALL will host a series of meetings designed to develop best practice from affiliates who have experience of these changes.
As well as a series of company-specific network meetings, an expert meeting on changes in the industry will be held this year. In December, this will culminate in an IndustriALL auto meeting where recommendations for dealing with changes in the sector will be discussed.